Do your printed parts not fit together or are they just not the right size? This may be because your printer is not calibrated well enough. There are some simple things you can try to counteract the problem.
Loose belts
If the belts on your printer are not fastened well enough, the printer will have difficulty holding the print head where it is expected. If there is a millimeter slack in the belt, your prints could be 2 mm too large in that axis. It's rare it's such large numbers but the idea is the same. Most printers have the ability for the belts to be tightened. Either by using a built-in tensioner or by loosening one or two screws and then typically by pulling the idler wheel.
Extrusion print factor
If your print multiplier is set too high, the plastic will tend to float out to the sides and create lines that are wider than they should be. Therefore, your walls on the model become thicker and form a larger part. Find a value that gets you as accurate wall thicknesses as possible without it ending up in underextrusion.
Step per millimeter
Proceed with caution; only do this if you're 100% sure nothing else (like over-extrusion) is to blame.
A 3D printer needs to know exactly how much a rotation of the motor result in one millimeter moved in the real world. This is called "steps per millimeter". On stepper motors that typically run our printers, a rotation is divided into steps that form a certain angle each. The printer needs to know how many of these steps it takes to move the axis of your printer 1 millimeter. If this number is not set correctly, the printer will think it should run longer or shorter than it should. It is usually easy to set in the menu on your printer, however it may well be tucked away a bit. You don't have to guess and test a number, there is a simple formula for finding the right number. It's easy to keep up with.
Print a box of 20 x 20 millimeters that has markings for X and Y so you can see which axis to measure (link here). Find the most accurate measuring tool you have, preferably a caliper if you have. Measure how big your box actually became. Let's say it is 20.5 mm on the x axis and you have found "steps / mm" in your printer menu. The current step / mm for the x axis is 40. Now we have all the numbers we need. Now they just need to be inserted in the formula below.
current steps/mm X original size of the x-axis / actual x size of the box = Your new step/mm value.
Example: 40 X 20 / 20.5 = 39
Your new step/mm value is inserted into the menu of your printer under the correct axis and can now be repeated for both the Y and Z axes. Print the box again and test if your result is closer to the desired size. Note that the new value should be close to the past value and if not; run the calculation again and make sure you put everything in exactly right.
Give feedback on the article
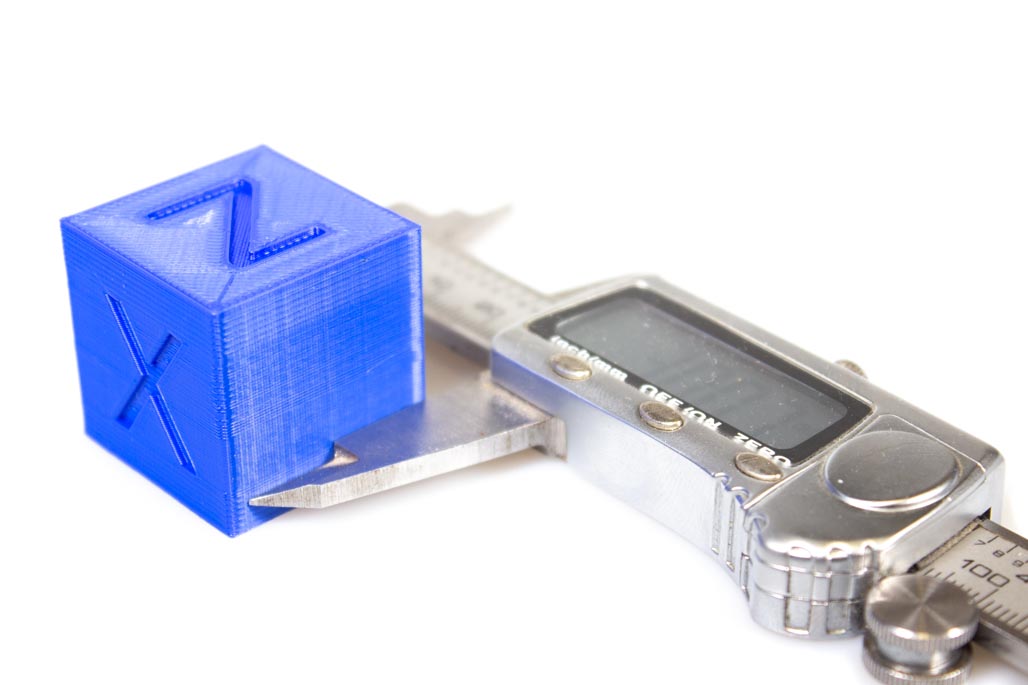
Published: Oct 2020, updated: Jan 2021